Metallurgy consulting
Inspiring metallurgy
InsPyro improves and develops metallurgical processes in cooperation with its customers. Our mission is to provide an efficient and targeted service, which leads to improved process understanding as well as improved profitability for the customer. Read some anonymized project examples below. Our experience includes steel production (including stainless steel and foundry) as well as processes for smelting and recycling non-ferrous metals such as lead, zinc, copper, aluminium, antimony, and rare earths.
Our services aim at answering your question efficiently and effectively. We evaluate our performance, and on average our customers give us a score of 9.3/10 for relevance of the results and 9.2/10 for quality and delivery speed.
The transition to a low-carbon society is speeding up and metallurgical industry is at the core. Metals are key to sustainable technologies, while the industry itself it transforming to use more sustainable technologies, energy sources, and recycled raw materials.
With our wide simulation and laboratory tool set, we tackle operational topics including:
- Improving metal yield and preventing losses
- Adjusting the process to different impurities in secondary raw materials
- Improving product quality, e.g. powder purity and particle size distribution
- Explaining and remediating process disturbances
- Decreasing dust generation as well as diffuse emissions
- Improving occupational hygiene, reducing risks of exposure to heavy metals
- Optimizing slag to reduce interactions with refractory and improve physical properties
- Improving slag mineralogy and treatment for reuse
- Reducing energy and reductant consumption and adjusting to new sources, such as hydrogen
To implement consulting recommendations, we strongly believe in providing process managers and operators with accessible models and recommendation systems, and our software does exactly that.
Our strategic consultancy aims at preparing our customers for the future:
- Finding unused capacity, current and future bottlenecks
- Defining processing routes and investment needs for raw materials and recycle streams, incl. capex/opex assessment
- Assessing techno-economic feasibility of expansions and new sustainable processes
- Lowering environmental impact, quantified by LCA, towards Green Deal targets or CO2-neutral production
Case study: process feasibility
A customer wanted to treat an industrial byproduct to recover valuable metals. Our mass and energy balances showed the requirements to reach separation, which was the start of selecting an appropriate vessel and technology. Thermodynamic calculations showed optimal temperatures for maximal separation, taking into account the melting points of the different phases. The customer has scaled up the process into a profitable business unit.
Case study: off-gas problem solving
A customer saw a change in the colour and physical aspect of the flue dust from a furnace. Our thermodynamics based mass balance explained the different composition and could trace it back to changed conditions in the furnace. Also the changed mineralogy of the dust could be predicted, and confirmed by XRD. These phases could be linked to problems in downstream hydrometallurgical dust treatment. Based on the model, limitations became clear and adaptations were suggested.
Case study: healthy work environment
After investing in automation technology, a customer saw an increase in dust emissions around the installations. He suggested modifications to the exhaust system, but wanted to know the extra suction volume needed. Our CFD calculations showed the potential as well as the limitations of the adapted concept, as well as the minimum fan size to reach a clean work floor.
Tools
The consulting work of InsPyro supports on three pillars, which are complementary to each other, and suit the needs of every project. First of all, we have calculations and modelling. Here, depending on the needs, we use thermodynamics, flowsheet models, or CFD. A second specialty are high temperature experimental set-ups. Finally, there is materials characterization and analysis.
Thermodynamic modelling and process analysis
Thermodynamic models are suitable tools to relieve some of the complexity of multi-component processes. Both for exploratory work as for process optimization, they can give a solid estimation of the expected equilibrium, phase compositions, metal yields, and so on.
InsPyro has a strong background in thermodynamics and metallurgical theory. We are highly flexible and can provide phase diagrams, process models, software tools, or materials interaction studies, always keeping the application in mind, and assisting in the interpretation and in implementing the implications.
The results of equilibrium calculations are compared to the actual process performance to find kinetic limitations and calibrate the models. Where necessary, we perform profound analysis of plant data or dedicated measurement campaigns.
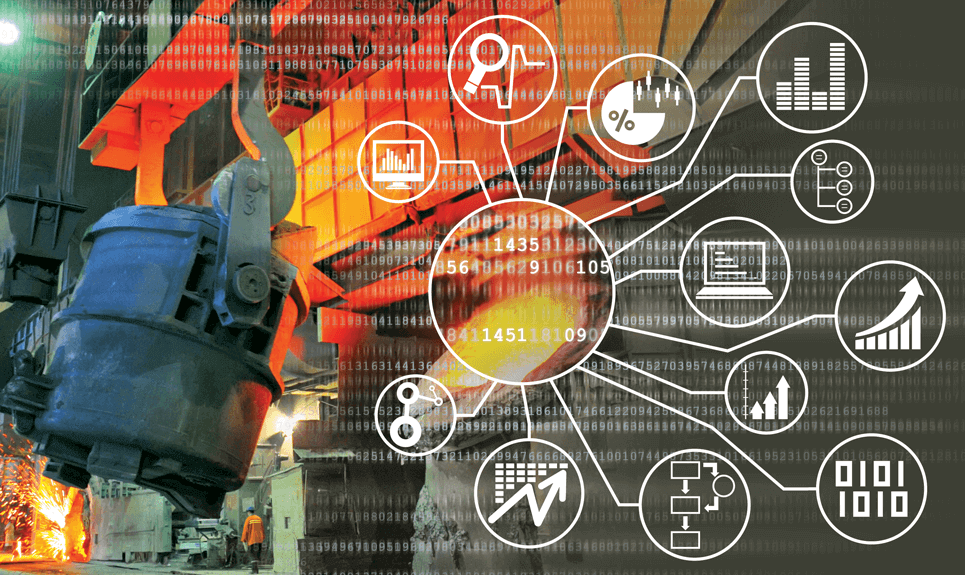
Flowsheet simulation
Flowsheet models deliver an overview at process or plant level, including byproduct treatment, auxiliary equipment and the like. Mass and energy balance can be built quickly and systematically, without limitations on the amount of component, recycle streams, and process steps.
In recent projects, InsPyro has built METSIM models for pyrometallurgical and hydrometallurgical flowsheets. In the design phase, these allow to estimate the energy need, and the need for fluxes, gases, and chemicals. For existing plants, models allow to optimize process decisions, such as pretreatment and bleed percentages, process settings, and control strategies.
Flowsheet models are also the basis for environmental impact simulation through life cycle assessment.
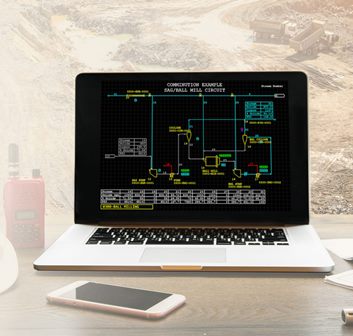
CFD modelling
With CFD, the flow patterns in a reactor or piece of equipment can be studied in detail. The technique allows to investigate:
- Temperature distribution in furnaces, e.g. to optimize the reactions in the bath or to avoid hot-spots on a refractory wall
- Flows in off-gas systems, such as cyclones, filters, etc., with the resulting particle removal, which allows to optimize the design
- Particle behaviour (e.g. flue dusts or fumed metals), including breakage, collision, and coagulation, and the effect on the particle size distribution function
- Ventilation design to guarantee safe and clean workspaces
- Effect of reaction speed and process parameters on the throughput
- Effect of design changes on operational performance, such as separation, mixing, or capacity
Visit our CFD page for more examples including applications outside metallurgy.
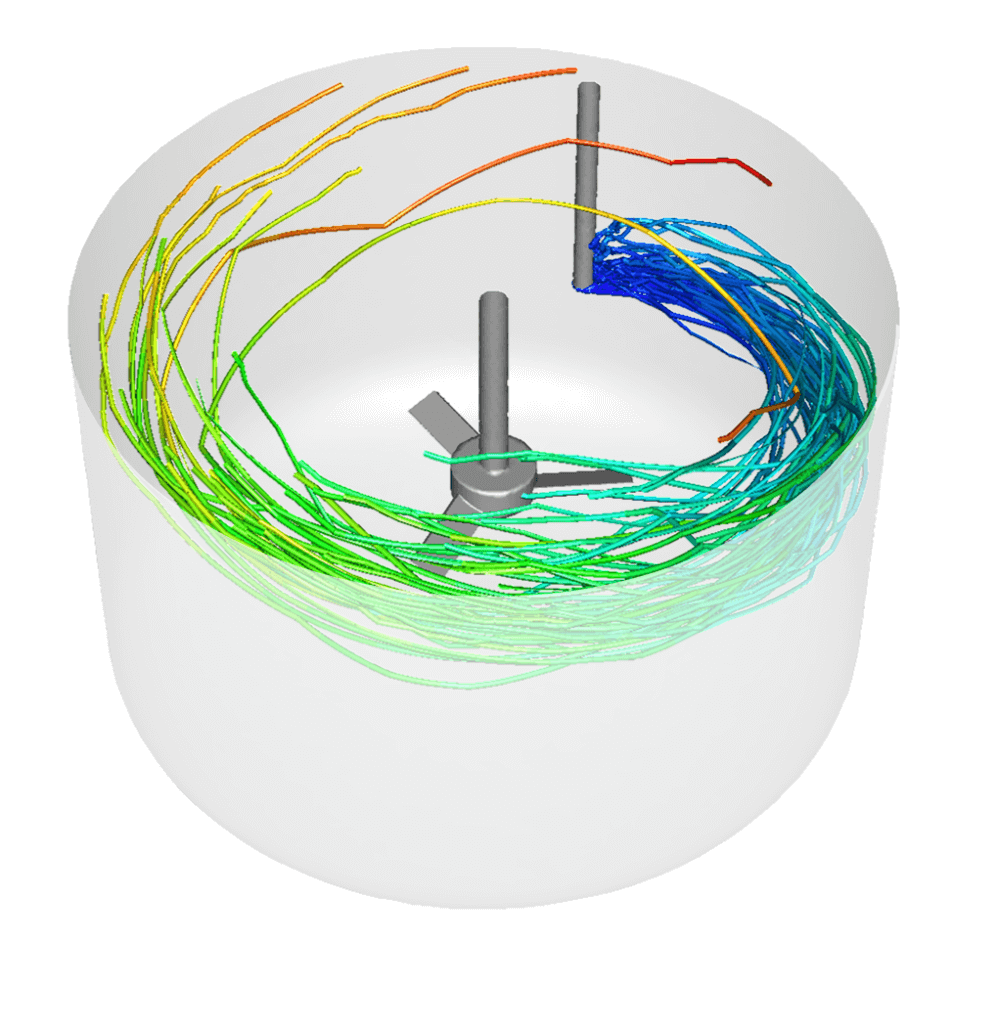
High temperature experimental set-ups
InsPyro has an extensive experience and the necessary equipment to perform several high temperature experiments. The scale ranges from below a gram up to 20 kg. The temperature can be as high as 1650°C. Different set-ups are available to study the interactions between refractory, metal and slag, as well as for solidification. Most set-ups rely on lab scale tube furnaces with controlled atmosphere, and induction furnaces at kg scale. A lab set-up for fluidised bed roasting is also available.
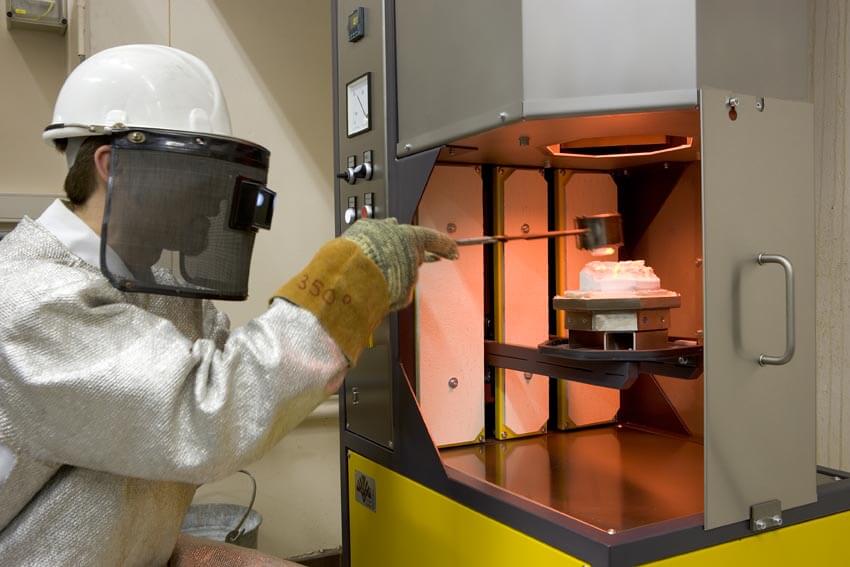
Materials Characterization
InsPyro opens up a range of characterization possibilities for your project:
- Microscopy and microanalysis: light optical and electron microscopy (SEM), EPMA, automated image analysis
- Chemical analysis and assays: XRF, XRD, wet-chemical, ICP-AES, ICP-MS
- Mineralogical analysis: quantitative phase composition with XRD-Rietveld, automated mineral classification with SEM
- High temperature characterization: heat, weight, size etc. as function of temperature with DSC, TGA, Dilatometry
A large range of techniques for sample preparation and mechanical characterization at low and high temperature is also available.
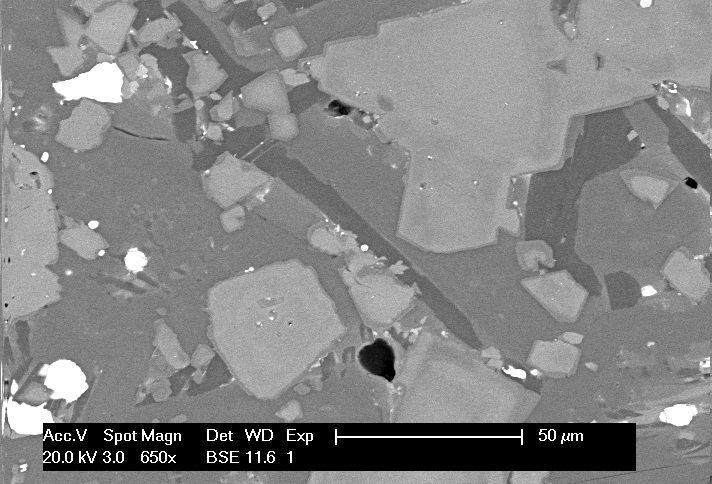
Reference customers for metallurgy consulting
Hereaus Electro-Nite
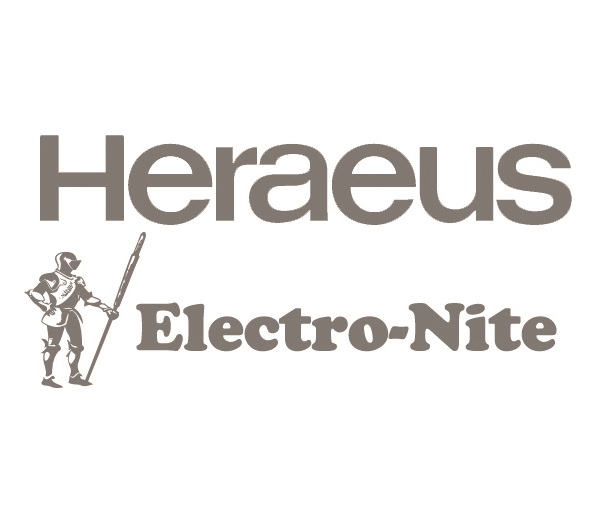
Rockwool
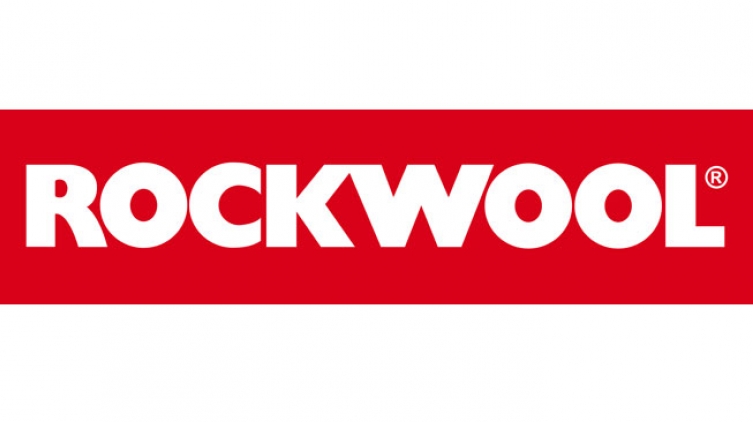
Boliden
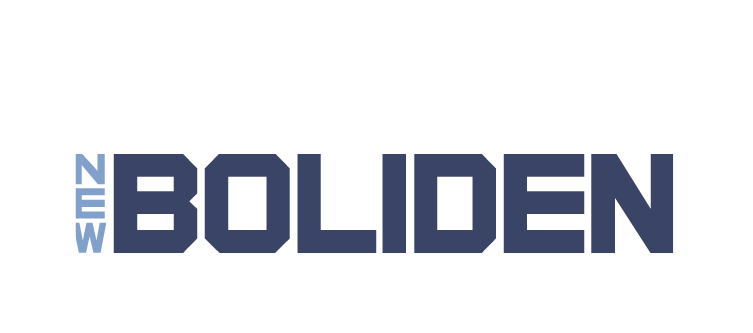
Aperam
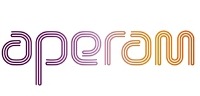
Aurubis

Ascometal

Magotteaux
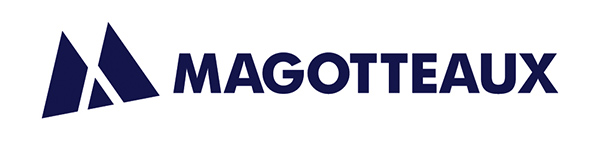
SMS Siemag
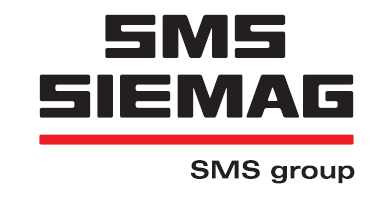
Nyrstar
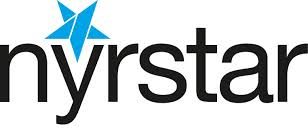
Berzelius
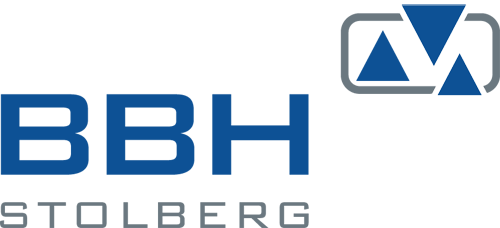
Campine
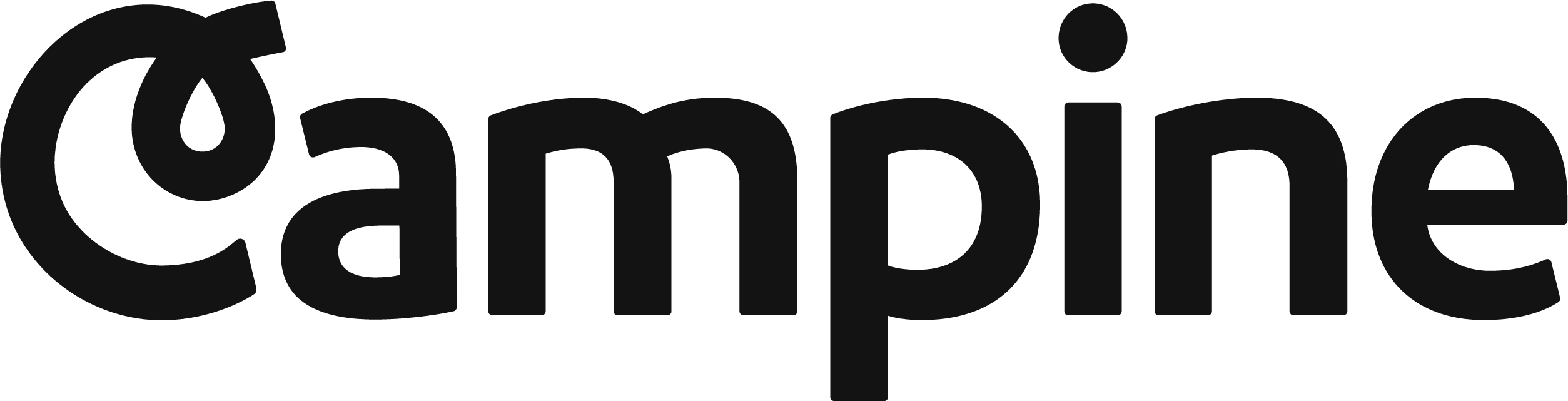
Recytech
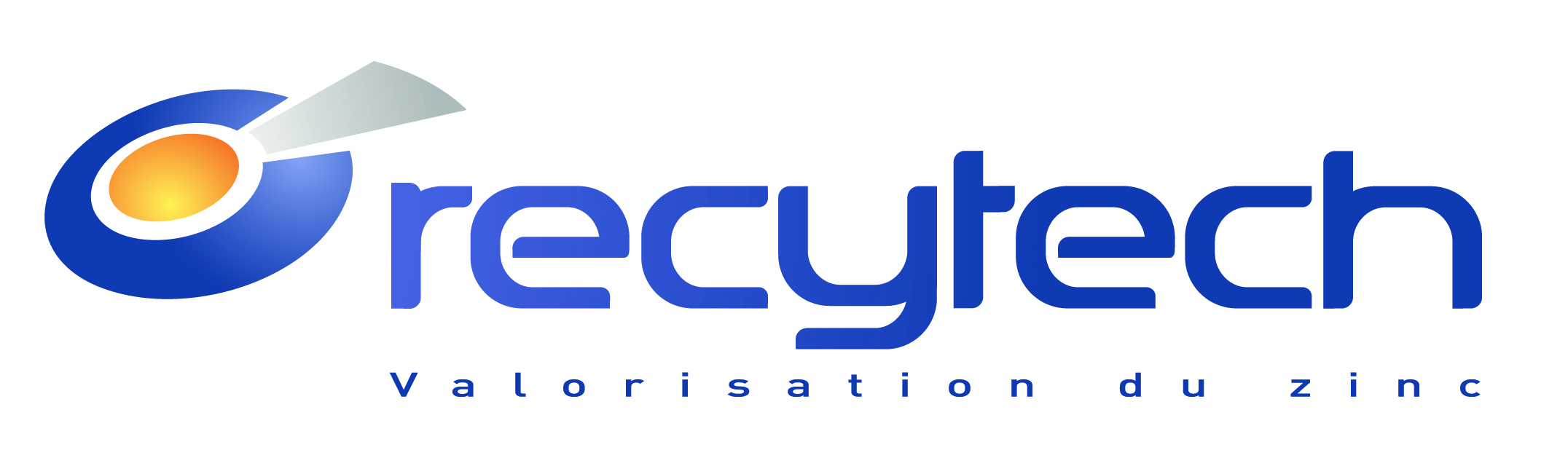