CFD simulation of furnaces
Furnaces operate at high temperatures and there are limited possibilities to run tests without affecting productivity or safety. CFD provides a powerful tool to study operational optimization as well as design changes, to improve energetic, environmental, and process performance.
As illustrated in the movie below, the fluid flow patterns in a furnace can be highly complex due to the turbulent interaction between burner combustion patterns and excess air flow. Modelling this fluid flow accurately forms the basis of quantifying the convective and radiative heat transfer. The simulation results in a detailed temperature and species (O2, CO, CO2, NOx…) distribution. Once the model is constructed and validated, several scenarios are simulated, aiming to improve certain aspects of the process:
- Heat distribution: Ensuring that heat is provided where it is needed, avoiding hot spots in the refractory, and increasing productivity along with energy efficiency.
- Combustion process: Increase combustion efficiency, especially towards reducing pollutants such as nitrogen oxides (NOx), particulate matter, and unburned hydrocarbons.
- Material production: The chemical and physical processes taking place in furnaces in metallurgical, chemical or glassmaking industry can be improved by improving heat transfer and mixing.
InsPyro has the experience of modelling several types of furnaces, such as short rotary furnaces, kilns, reverberatory furnaces, and other types of gas or oil fired installations. Our expertise is equally valuable for electrically heated furnaces, bath smelting furnaces, ladles or post combustion chambers.
Most simulations are run in steady-state, but transient analysis can be performed for start-up, shut-down or varying loads to understand the furnace performance under dynamic conditions. Feel free to contact us to discuss possibilities.
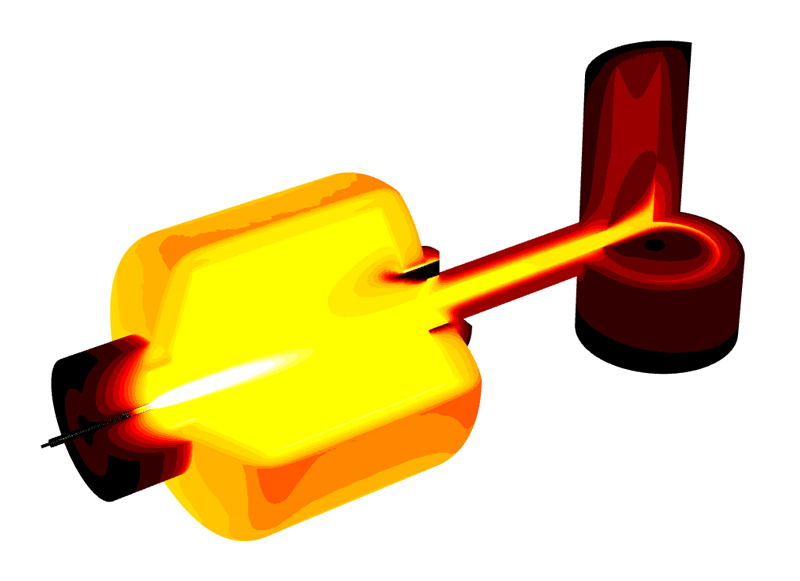
